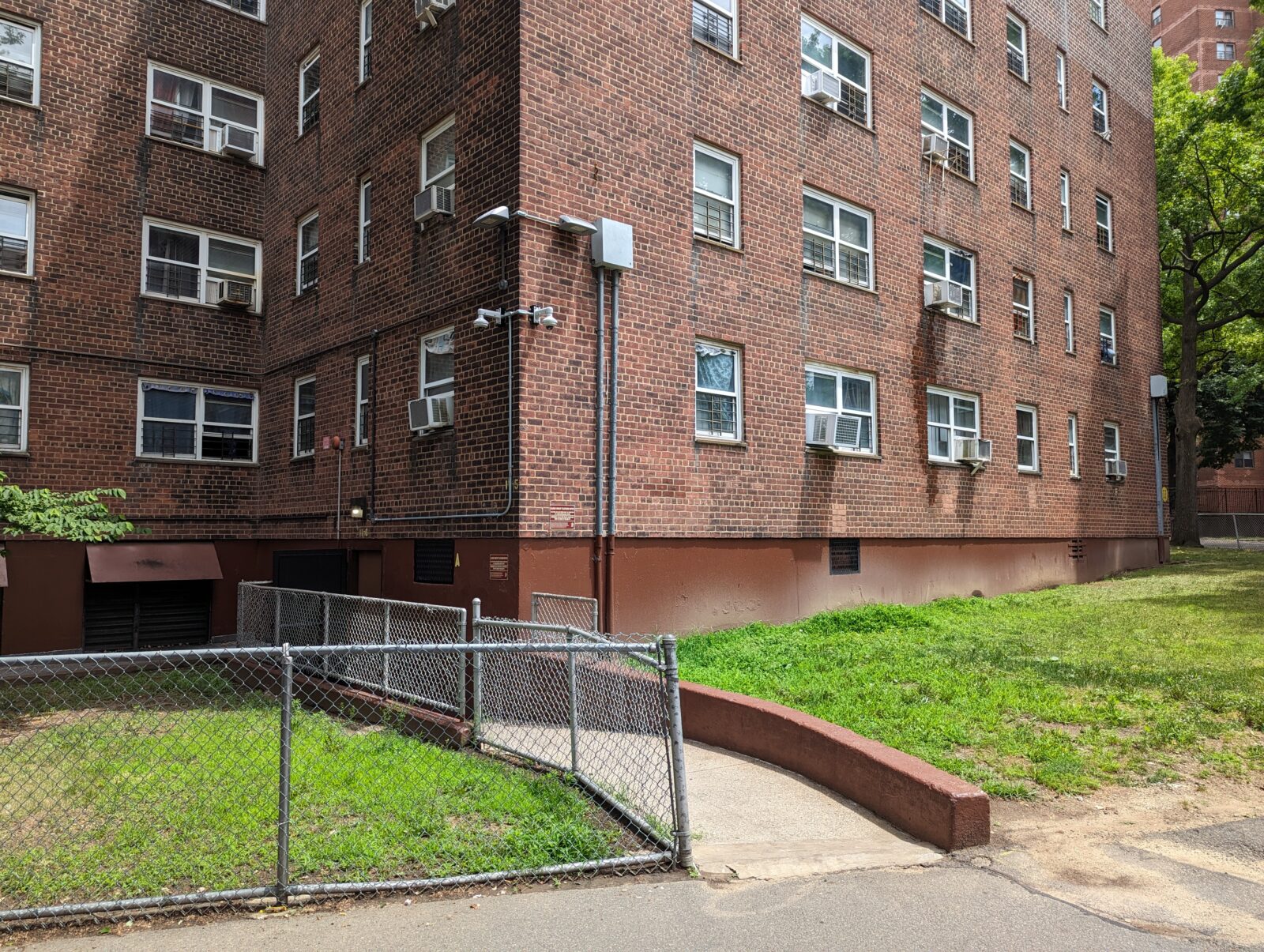
Description
- The majority of NYCHA’s buildings are clad in masonry, typically common clay brick. Depending on the age of the development and the particular design the brick masonry exterior walls can be brick with CMU backup, brick cavity wall, or multi-layer (wythe) solid brick construction. In addition to masonry,
manysome buildings and structures utilize a variety of durable cladding materials like stone, terra cotta tile (especially at parapet copings and entrances), glazed or split-face concrete masonry units (CMU), and concrete (particularly at the exposed foundation walls and entrance canopies). Most surround reinforced concrete or steel frame interiors, but there is a wide variety of building details tying the existing brick or cladding to the building structure. Except for some pre-war tenement buildings owned by NYCHA, most buildings have little if any exterior ornament. These materials require maintenance and repair to maintain the integrity of the thermal envelope and to eliminate moisture transfer to the interior. It is also critical to maintain facades and repair deterioration or structural defects for the safety of residents and general public. - Aside from PACT or COMPMOD projects (described below) most NYCHA brickwork and cladding projects involve repair of existing facades. There has been patchwork maintenance to the brick cladding, but few comprehensive exterior upgrades. When replacing brickwork and cladding it must first be thoroughly inspected for defects and structural issues by a Qualified Exterior Wall Inspector (QEWI) as specified by NYC Local Law 11 and requirements in NYC Building Code. With extensive brickwork or cladding upgrades, it is important to use any invasive or other required survey techniques such as physical probes, drones to examine the upper floors, infrared to determine areas of water penetration or heat loss, or radar to verify any bowing that could indicate settling or structural deterioration. The more information gathered up front on the existing cladding and details the more accurate the scope of work and project schedule. Additional building exterior repairs may include parapet removal with railing replacement, rooftop elevator machine room and roof stair bulkheads, and water tank enclosures. Most brickwork upgrade projects require scaffolding and sidewalk sheds. It is important to coordinate the scaffolding, sheds, and any other safety measures with the permitting process and with the development stakeholders.
Baseline
- Pointing – Masonry walls frequently deteriorate at the mortar joints. When this happens, loose and damaged mortar must be thoroughly removed from the exterior face of the joints and replaced. Improper pointing can compromise the structural integrity of the masonry and undermine the performance of the facade. New mortar must match the original mortar in compressive strength, vapor permeability, color, texture, and tooling to the maximum extent possible. Bricks or patches of bricks can also experience cracking or spalling due to impact or freeze/thaw cycles. In those instanced skilled brick replacement or stitching to match the existing would be required. These guidelines should also be followed when brick infill is required in patches due to removal of through-wall ductwork, conduits, piping, HVAC machinery, etc.
- When designing a brick repair project the first step is to verify the type of exterior wall with the NYCHA archived drawings. But it is also important to verify existing conditions in the field, since what was drawn might not match what was constructed, and subsequent repairs or upgrades might not be incorporated into the drawings or recorded in the archives.
- Masonry repair might also be required due to uneven settling or separation at the building corners, or frequently as part of other upgrades such as window replacement. If vertical cracks across brick courses or step cracks are present, the design could require installation of new vertical or horizontal expansion or control joints. These should be located carefully depending on the visibility of the facade. Very often insufficient drainage over windows will result in rusting of the steel lintels or shelf angles and subsequent damage to the brick coursing. This will require removal of the brick over the windows to facilitate replacement of the steel angles, and that will require hazmat testing for lead-based paint if the steel is painted or asbestos-containing materials (ACM) if the window caulking tests positive. In those instances the brick repair project could require abatement and coordination with the residents. If there is brickwork or cladding damage due to interior issues such as structural deterioration those conditions need to be verified and addressed as part of the project. It’s important to try and avoid masonry upgrades as a cosmetic cover for underlying issues that will manifest themselves over time and damage the new brickwork. Brick deterioration can also occur when weepholes were either insufficient in the original construction or have become clogged over time. This should be verified and corrected as part of the cladding upgrade.
- Brick Replacement – In addition to matching structural characteristics, new masonry must also match the original in color, texture, and size. Since most masonry facades are cleaned rarely and brick color will naturally weather and darken over time, before initiating the project work create brick and mortar reference
smock-ups by cleaning an area (see photo). Multiple brick/mortar mock-ups might be required to find the proper match. Note that different elevations of the building may weather or deteriorate unevenly due to exposure to sun and precipitation, so brick and mortar replacement may require different shades. Ensure that replaced brick and mortar match the cleaned patches of the walls. In many developments, subtle design details in the original masonry were constructed with specially shaped or placed masonry units; these features should be replicated as part of the rehabilitation. It is important to avoid contrast between the repaired areas and original brickwork which detracts from the appearance of the building. It might be possible to include facade cleaning and mold removal as part of the base contract work. - Parapet Walls and Other Roof and Wall Elements. (Note: masonry should not require frequent upkeep.) Masonry at the parapet walls carry added importance, as they prevent water infiltration where the roof meets the facade. For more cost-effective and longer-lasting rehabilitation, NYCHA has moved away from repairing or replacing masonry parapet walls where possible and now removes the parapets and installs easy-to-maintain metal rails during roof rehabs (see photo and Office of Design sample detail). This very often requires replacing several brick courses below the roof line, typically down to the upper row of windows. NYCHA has worked closely with NYC Department of Buildings to identify appropriate treatments for the removal and reduction of brick rooftop structures, such as long-dormant smoke rooms and a height reduction of what used to be incinerator stacks. These flues now generally serve as trash chutes that connect to garbage compactors. Many of these projects can require patching to the roofing. In such cases it is important to verify that no brickwork would violate any current roofing warranty. (Note: recommend including photos of both good and bad brick stitching for examples.)
- Frequently there are existing facade elements such as balconies or fire escapes that must be maintained and accessible during the course of brickwork or cladding upgrades, and these need to be incorporated into the project timeline. There are also surface-mounted utility items such as conduits, piping, electrical risers, antennas, lighting, or ductwork that need to be maintained and could affect access to the affected cladding to be repaired. If any relocation or temporary removal of any utility service is required it needs to be coordinated with the stakeholders and any applicable service provider and necessary repairs due to anchor removal, etc., incorporated into the scope of work.
- In the case of multiple materials, either in the wall section or elevation, repair all existing building envelope components, including exterior masonry and concrete as needed. In areas of consistent water penetration, investigate the possibility of using a breathable penetrating masonry sealant at any façade with exposed masonry. Tuck pointing at the exterior and air-sealing all façade penetrations can also be used to maintain or improve airtightness, but this is not used as frequently as standard pointing. Use of tuck pointing should be verified with the NYCHA representative and the stakeholders as it affects the building’s appearance. All new or existing penetrations must be sufficiently weathertight and in the case of rated walls the existing fire rating must be maintained.
- Filing: Depending on the size and scope of work and whether the buildings is located in a designated FEMA flood zone, the brickwork or cladding project might require filing with the Department of Buildings. This should be verified as early as possible, and all necessary sub-contractors or vendors for third-party inspections included in the budget and timeline. Also verify any historic preservation requirements. Few NYCHA developments are designated historic landmarks, but more are subject to review by the State Historic Preservation Office (SHPO), so this should be determined by researching the SHPO National Register of Historic Places and NYC Landmarks Preservation Commission Database accordingly to verify if this restricts any design possibilities.
- Design: It should be noted that not all brickwork or cladding upgrades are limited to repairs or replacing in kind, and visual design upgrades can be included as well along with goals of reducing carbon footprint of buildings.
- Sustainability: Wherever possible brick, CMU, mortar, etc., should be locally sourced and sustainable materials used. Fine aggregate in mortar, for instance, was typically beach sand in older buildings, but this is a depleted resource so manufactured aggregate should be substituted, as stated matching the color as much as possible. Where brickwork on an elevation extends down to grade, all materials and details should be designed to withstand flooding due to climate change, especially at developments on the waterfront and/or within designated FEMA flood zones. This could entail additional reinforcement within the walls or additional exterior coatings, or possibly an applied exterior material at the lower courses. Recycling should be incorporated into the project as much as possible. Removed bricks have traditionally been discarded to landfill, but there is a growing move to provide bricks for recycling, and this should be incorporated into the contractor’s waste management plan. Where possible it is highly desirable to install exterior insulation in a cavity wall.
Stretch
Note: For the Stretch section on cladding, PACT and COMPMOD projects are not designed or overseen by AES. They should still comply with NYCHA standards and Basis of Design requirements, especially regarding sustainability and stakeholder engagement.
- Provide full envelope upgrades (all enclosure walls) with interior or continuous exterior insulation (with Masonry Back-Up Waterproofing). [COMPMOD]
- When selecting a cladding system, prioritize non-combustible insulation and overall fire resistance, durability, and thermal and moisture performance.
- Cladding a building in new material(s) represents an opportunity to greatly increase the appearance of the elevations, for the stakeholders and the neighborhood. Cladding a building in a single new material is typically the most cost effective and expedient, but NYCHA buildings are often of multiple heights, footprints and massing, so multiple materials might be possible, for instance an impact-resistant masonry at the lower floor(s) and a rain screen above. EIFS often lend themselves to varied color schemes. Stakeholder engagement in investigating the possibilities and finalizing the design is essential.
- Include cut sheets and warranty information for specific products.
- Teams can propose and price an adhesive applied EIFS (Exterior Insulation and Finish System) product if they choose, but should also propose and price an alternative, prioritizing rain-screen cladding systems with continuous insulation.
- Options for rain-screen finish panels include but are not limited to fiber cement, composite, and metal panels. Any panels susceptible to cracking upon impact or absorbent for graffiti should be mounted outside of standard reach range.
- If EIFS, or any other face-sealed (adhesive-applied) barrier wall system is specified and priced, describe assumptions for moisture management components, drainage provision, and inspection, maintenance, replacement, and removal protocols in detail.
- Envelope upgrades may not need to ensure thermal performance to code minimum, but clearly this is desirable. Passive House standards should be utilized as a standard wherever possible. Also verify if certain elevations of a building could require greater insulation depending on building orientation or shade, etc. [COMPMOD]
- Describe moisture management strategy and components. [COMPMOD]
- Assume a breathable masonry coating at any façade with exposed masonry.
- Interior Insulation – Where feasible and appropriate for adequate mechanical system sizing, thermal comfort, and airtightness, assume full envelope upgrades (all enclosure walls) with interior insulation. Options could include blown insulation in cavity wall or thin insulation installed on the interior of the apartments and covered with a layer of gypsum board. System options include but are not limited to rigid, blown-in, loose-fill, batt, wall board, or an integrated sheathing system. Installation approaches include but are not limited to loose-fill or blown-in insulation in existing cavities, if assumed; Wall board or sheathing at the interior face of existing interior envelope walls; New, furred out walls at interior with insulation between studs; Existing cavity walls can be removed and rebuilt, or can remain.
RAD Conversion
Exterior Walls and Facades
- Assume that full envelope upgrades (all enclosure walls) are necessary to improve building performance, reduce energy usage, and ensure resident comfort.
- For consolidated developments with diverse typologies and existing conditions, varying approaches to building envelope upgrades will be appropriate and acceptable for different typologies within the consolidated or scattered site group.
Opaque Wall Enclosures
- At minimum, all existing building envelope components should be repaired, including exterior masonry and concrete as needed. Assume a breathable penetrating masonry sealant at any façade with exposed masonry where feasible. Tuck pointing at the exterior and air-sealing all façade penetrations is also required to improve air-tightness.
Additional improvements may include:
- Interior Insulation:
- Where feasible and appropriate for adequate mechanical system sizing, thermal comfort, and air-tightness, assume full envelope upgrades (all enclosure walls) with interior insulation.
- System options include but are not limited to rigid, blown-in, loose-fill, batt, wall board, or an integrated sheathing system.
- Installation approaches include but are not limited to loose-fill or blown-in insulation in existing cavities, if assumed; Wall board or sheathing at the interior face of existing interior envelope walls; New, furred out walls at interior with insulation between studs; Existing cavity walls can be removed and rebuilt, or can remain.
- Consider how lead removal strategy may impact building envelope improvement scoping.
- Interior envelope upgrade solutions do not have to assume thermal performance to code minimum. A strategy should be identified to evaluate existing envelope condition, air-tightness, and R-value, and identify target performance metrics that will allow adequate mechanical systems sizing and support a selected ventilation strategy.
- When selecting an insulation product non-combustible insulation should be used and fire resistance as well as thermal and moisture performance should be prioritized.
- Exterior Insulation and Cladding (“Over-cladding”):
- Where feasible, assume full envelope upgrades (all enclosure walls) with an exterior continuous insulation and cladding system for all buildings not under consideration for historic tax credits or already National Register listed or eligible.
- System options include pre-fabricated and/or pre-fenestrated panelized systems (Dextall D-Wall or similar), insulated metal panel systems, rainscreen systems with continuous insulation, exterior insulation and finish systems (“EIFS”).
- When selecting a cladding system, non-combustible insulation should be used and fire resistance, durability, and thermal and moisture performance should be prioritized.
- An adhesive-applied EIFS product can be proposed if selecting a product that uses non-combustible insulation.
- If an EIFS product is proposed, an alternate system and product should be included, prioritizing rainscreen or pre-fabricated panelized cladding systems with continuous insulation.
- Options for rainscreen finish panels include but are not limited to fiber cement, composite, and metal panel.
- If EIFS or any other face-sealed (adhesive-applied) system is specified, describe moisture management components, and summarize on-site installation quality control protocols for any product that relies on adhesive lines for back-draining.
- If EIFS or any other face-sealed (adhesive-applied) system is specified, a preliminary lifecycle cost analysis must be submitted that describes inspection, maintenance, replacement, and removal protocols in detail.
- Re-point and repair existing brick before installing any over-cladding system to ensure the existing façade is in sound condition.
- Assume thermal performance to code minimum.
- Consider tamperproof access panels for equipment, conduit, or piping mounted between the existing façade and new cladding.
Strategies
Promote Safety and Security of Residents & Staff
Optimize Performance, Operation & Maintenance of Buildings, Systems & Assets
Last Updated on May 8, 2025 at 2:20 pm
Downloads and Data
Specifications
Details